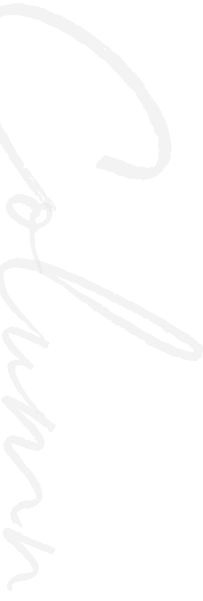
fi’zi:k | 世界初の3Dプリントサドル アダプティブ #02
- fi'zi:k
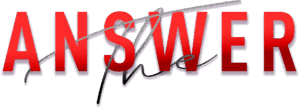
イタリアのフィジーク本社でAM Global Business Managerを務めるニコラ・ポレッティ氏と、フィジーク誕生のルーツや、過去から現在地への道すじを辿ったあとは、その製品ラインナップの中で、近年ひと際輝きを放つ3Dプリントサドルのアダプティブについて訊いた。今や多くのメーカーが手掛ける3Dプリントサドルだが、世にはじめて登場した3Dプリントサドルがフィジークのアダプティブだ。
Question.
いまや、多くの3Dプリントサドルが登場しているが、パイオニアであるアダプティブとは?また、その特徴と優位性は?
3Dプリントサドルのパイオニアであるフィジークは、どのような背景がありアダプティブの開発に至ったのか。なぜ、3Dプリントなのか。#02では先進の3Dプリントサドル・アダプティブのアンサーを探る。
#02 ADAPTIVE
ニコラ・ポレッティ氏の案内で、ファクトリー内を歩いていると、様々なバリエーションのサドルが生産されている。フィジークは形状やレール素材、ベースシェル素材の違いなどで、非常に多くのサドルラインナップを持つ。その多くがスタンダードなフォーム・パッドを採用したサドルだ。ロードバイクを駆るライダーだけでなく、厚みや柔らかさに違いはあれど、シティサイクルにも採用されていることから、最も一般的に知られている素材と言っても差し支えないだろう。

サドルの製造は、多くの工業製品と同様、ライン生産方式によって進められる。ファクトリー内にはジェットコースターのような製造ラインが縦横無尽に駆け巡り、その上をサドルやベース金型がひっきりなしに流れていく。ベースの成形、フォーム素材との貼り合わせ、表皮の接着、最終的な仕上げ処理。工程を経るごとに、「素材」が少しずつ「製品」としての形を帯びていく。そして、随所で熟練の職人たちの手作業が入り、フィジークのディテールとDNAを宿していく。

工場内を案内されながら奥へ進むと、少し隔離された一室に大型の3Dプリンターが静かに佇んでいた。ここでは、フィジークがいち早く手がけたアダプティブ・サドルの3Dプリントパッドが成形されている。残念ながら取材時には稼働していなかったが、すべてのプロセスがこの場所で完結しているという事実は、それだけでも印象的だった。
THE ANSWER編集部(以下TA):フィジークは他社に先駆けて3Dプリントサドルを開発しましたが、製品開発のきっかけを教えてください。
ニコラ:アダプティブがデビューしたのは2020年です。今や、世の中には3Dプリント製品がたくさんありますが、その当時はまだ草創期で、特にサドルに関してはどこも手をつけていませんでした。でも、我々は「これはサドルの未来を変えるかもしれない。」という直感があり、どうやって製品に落とし込んでいくか、すぐに調査・研究をスタートさせました。
TA:という事は開発の時点では、どのような製品に落とし込むことが出来るかは手探りだったという事ですか?
ニコラ:そうとも言えますが、3Dプリントでパッドを製造すれば、スタンダードなサドルに採用されるフォーム素材とは異なり、サドルの部位に応じて、自由に密度やパターンを変更することができることは分かっていました。つまり、体重を支える箇所はしっかりとした構造体を、特に支える必要がない部分は密度を抑えて乗り心地を良くする、といった具合にね。それも、体重を支える部分はセルの構造を変えて、耐久性を上げると同時にクッション性も良くなるような方法をとることだってできる。スタンダードなフォームを組み合わせることで似たようなことはできますが、3Dプリントのような緻密なコントロールはできませんし、接着部分に不具合が出たり、重量も重くなってしまいます。

アダプティブの開発目標は、快適性を向上させること。その名の通り、身体にアダプト(適応)させることをモットーとしています。緻密なプレッシャーコントロールを持たせることでサドルと身体の接触面積を増やし、ピンポイントで体重が乗らないようにすることで、快適性が飛躍的に向上するのです。ある測定では特定の部分で50%以上も圧力を分散させることができた、というデータを得ることができました。
アダプティブ・サドルを開発する上で、我々は3Dプリンターのパイオニアであり、アディダスとコラボレーションして、3Dプリント・ミッドソールを作っていたアメリカのカーボン社、そしてフィッティングのスペシャリスト集団であるゲビオマイズドとの協力体制を築きました。結果的に素晴らしいものができたと思いますし、他社が続いているのは、その証拠であると考えています。
TA:では他社の3Dプリント・サドルに対しての優位点はどこだと考えますか?
ニコラ:今や多くのブランドから3Dプリントサドルが出てきましたが、我々から見ると「ただ3Dプリント・パッドをつけただけ」のサドルも少なくありません。様々なサイクリストの圧力分布データを計測し、それらを基に導き出した形状と密度を緻密にコントロールし、サドルの各部分に求められる機能をしっかりと与えているのは、我々がいかにこだわって開発しているかの証拠です。サドルの部位ごとに緻密にクッショニングをコントロールしてこそ、3Dプリント・パッドの真価が発揮されるのです。

TA:その先見性は、ついにカスタムサドルを作るという境地に達しましたね。2024年にデビューしたOne-to-One*1 について教えてください。
*1 専用の圧力マッピング計測装置を利用し、そのデータを基にオーダーメイドの3Dプリント・サドルを制作するサービス。
ニコラ:One-to-Oneのサービスを開始したことで、アダプティブは更に飛躍を遂げました。One-to-Oneは自転車とサイクリストのコンタクトポイントの中でも、もっとも個人差の大きなパーツであるサドルを、ついにカスタムオーダーできるようにしたことで非常に革命的なサービスであると言えます。
例えばOne-to-Oneで同じヴェント・アルゴをオーダーしたとしても、私とあなたでは出来上がった製品は全く違うものになりますし、計測で得られた圧力マッピングデータは今後のサドル開発に非常に役に立ってくれると期待しています。例えばアメリカでは160mm幅のニーズが高く、ヨーロッパでは140mm幅のニーズが高い、といったように、国が違えば求められるサドルも変わりますし、それを的確に製品に落とし込むことができる。

イノベーションとテクノロジーをライダーにフィットさせるというフィジークのフィロソフィーが最もよく象徴され、デザイン、快適性、そしてパフォーマンスを実現したプロダクトだと考えています。
TA:アダプティブと通常モデルの販売率はどのくらいでしょう?
ニコラ:アダプティブの販売率は「00」や「R1」といった、特にハイエンドカテゴリーのサドルと対比するとおよそ30~35%ほどです。一方で、サポートチームのプロ選手たちの割合を見ると、アダプティブの使用率は上がります。

これは、プロ選手が特に6時間近い長距離レースで、絶えず高いパワーを出し続けているから。つまりは快適性とペダリングのサポートの両方を求めるニーズが非常に高いということの証明でもあります。もちろん彼らにもOne-to-Oneサドルのオプションを用意していますが、フィッティングに問題がなくスタンダードなアダプティブを使う選手も多いんです。とにかく、快適であればあるほどレースに集中して、高いワットを出し続けることができる。これは成績を出す上ではメリットでしかありません。

TA:プロ選手と言えば、UAEチーム・エミレーツ・XRGとタデイ・ポガチャルは、今年からフィジークを使用していますね。ポガチャルはアダプティブを使っていますが、One-to-Oneのカスタムメイドですか?彼から製品についてどんなフィードバックがありましたか?
ニコラ:私はスポーツ・マーケティングのセクションではないので、彼と直接会話していませんが、反応はすごくポジティブだったと聞いています。たしか、当初彼には2~3点ほどカスタムモデルを作りテストしてもらいました。
シーズン序盤、ロードバイクではアルゴ 00 アダプティブを使い、その後通常モデルのアルゴ 00と併用しています。好みやコースに応じて変更しているようですね。
ツール・ド・フランス2025では、One-to-Oneでカスタマイズしたアルゴ・アダプティブを使用しています。また、タイムトライアルでは一貫してOne-to-Oneのアエリス LD アダプティブを使っています。

Answer.
密度や形状を細かく調整可能な3Dプリントテクノロジーを最大限活かしたアダプティブは、フィジークのラボで計測した膨大なデータを基に、各部位ごとに最適なクッション性を再現。これまでのフォーム・パッドでは実現不可能な快適性とサポート性を持ち、すべてのサイクリストにおすすめできるゲームチェンジャー。
#03へ続く
PHOTO & INTERVIEW: So Isobe – Cyclowierd
EDIT: Hirofumi Fukuda